Using metal powder in 3D printing is a very common practice in the aerospace, defense, and shipbuilding industries. It is used to provide physical properties such as strength, rigidity, and elasticity. However, using metal powder in 3D printing poses some challenges due to the particle size, shape, and storage. Fortunately, there are a few basic principles you can use to avoid problems in your process.
Basic principles
Compared to 3D printers that use plastic filaments, powder-based 3D printing is a relatively new technology. However, it has already proved to be a viable technique for many industries, including manufacturing and aerospace.
The most common materials used for 3D printing are aluminum and steel. These two materials offer good resistance and surface finish. 3d printing powders that can be used include nickel steel and gold.
Another popular material for 3D printing is stainless steel. These metals can be used in prototypes and other forms of functional parts. In addition, they have the ability to produce tough prints and bendable objects. These prints can be used in a variety of applications, including phone covers and wristwatches.
The most common metal powder 3D printing methods are Direct Metal Laser Sintering (DMLS), Direct Energy Deposition (DED), and Powder Bed Fusion. These technologies use a high-power energy source, such as a laser or electron beam, to melt and fuse the metal powder layer by layer. The intensity of the beam can be adjusted to suit the properties of the finished part.
Particle size and particle shape
During metal 3D printing, the particle size and shape of metal powder affects the quality of the end product. A metal powder with low particle size and round shape can produce a dense product with good mechanical properties. On the other hand, irregularly shaped particles can cause defects.
To determine the particle size and shape of metal powder, a variety of techniques are available. However, the most common techniques are based on two-dimensional measurements.
Two-dimensional measurement techniques include X-ray computed tomography (CT) and scanning electron microscopy (SEM). The former technique is used to evaluate the shape of powders that have a diameter on the order of several 10 mm. The latter technique uses light scattered from particles. This technique has limited field of observation.
Storage and handling challenges
Keeping a metal powder in a metal container can be a daunting task. Luckily, a well thought out system can keep the mess under control and minimize waste. The best part is that it can also help your bottom line. You can even use a robot to aid in the process if you have a big budget.
In order to keep the powder cool and contained, a small electric pump is used to maintain a steady temperature and containment. This enables you to get your metal powder to the right temperature at the right time. The system can even help you with the metal part finishing tasks. The small jar is also a perfect place to store the machine.
A good 3D printer should be equipped with a well thought out system that helps ensure the safety of the powder. Similarly, a robot can also help with the part finishing tasks, thus reducing your labor costs.
Physical properties
Choosing the right metal powder for 3D printers can affect the performance and efficiency of the process. According to Equispheres, the wrong choice of powder can lead to a weaker product and lower production speed.
The physical properties of metal powder in 3D printing are determined by the size distribution of the particles. Generally, the average grain size of metal powders ranges between 10 and 50 microns. This particle size is essential for the density of the final product. However, the shape of the particle also plays a role. Depending on the shape of the particle, the final product can be dense or porous.
The sphericity of the metal powder is also important. This characteristic is required for smooth flow inside the 3D printer. However, when the sphericity of the particle is too low, the density of the final product will be lower.
Aerospace, defense, and shipbuilding industries
Among the many applications of metal powder in 3d printers is in the aerospace, defense, and shipbuilding industries. These industries often employ metals such as aluminum, titanium, and tool steels to fabricate components. They also use these materials for repair and repurposing of old components.
In the aerospace industry, AM technology can improve cost, material utilization, and processing time. It can also increase component specifications. In addition, it can reduce material wastage and improve internal microstructures.
However, the aerospace industry has not yet been able to fully utilize AM technology to its fullest potential. There are a number of challenges, including lack of part-driven data and lack of technical standards.
One of the main issues in metal AM is process repeatability. This is a result of the high growth rate of metal AM technologies in recent years. However, major governing bodies have developed increasingly stringent testing protocols and certification steps. These measures will help ensure consistency in the AM-fabricated aerospace components.
Metal Powder in 3D Printers
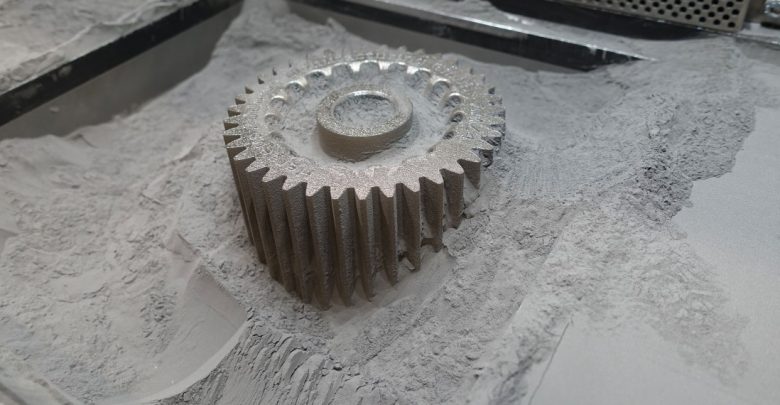
More Stories
Most Popular Auto Shows Across The United States
PCD Pharma Franchise in Panchkula
Becoming a Pharmaceutical Distributor with Aenor Pharmaceuticals